エネマネ事業者を活用し、補助金を受けた電炉メーカーの設備投資案件
電炉メーカーの東京製鐵は、岡山工場の大規模設備投資でアズビルをエネマネ事業者として活用し、平成27~29年度の「エネ合補助金」で1/2の補助金の採択を受けた。複数年にまたがる大規模工場(年間原油換算エネルギー使用量1,500kl以上)案件で、多くの実績を誇るアズビルの強みである省エネ制御を十分に発揮。東京製鐵は、今回増強された設備を活用し長期環境ビジョンに掲げた削減目標の達成と、電炉鋼材(低炭素・循環型鋼材)の増産を目指す。
大規模工場でのエネマネ事業者の活用が容易になるバウンダリーでの申請についてなど、今年度の変更点をまとめた『エネ合補助金の変更ポイント』資料を環境ビジネス限定で無料公開しています。こちら、もしくは文末より資料ダウンロードできます。
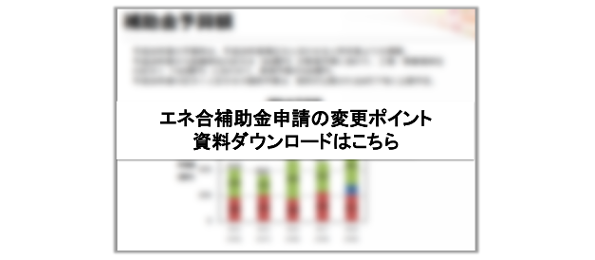
総額70億円のビックプロジェクトがスタート
2015年9月、電気炉メーカー最大手の東京製鐵は、今後の増産計画の鍵となる岡山工場への大規模な設備投資を決定し、3カ年にわたる巨大プロジェクトが動き出した。東京オリンピック後の景気収縮をにらみ、生き残りを賭けこの時期に設備増強を決断した。
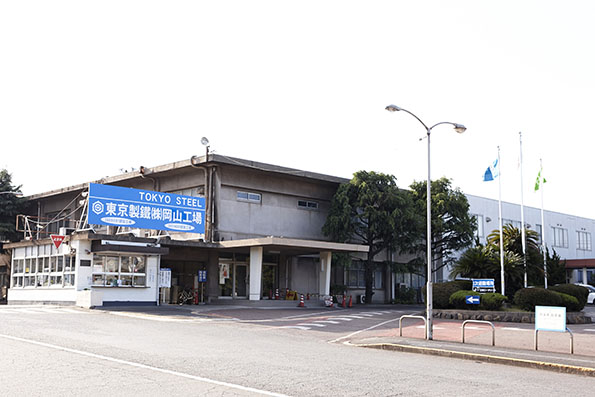
電気炉による製鋼は、原料の鉄スクラップを超高温で溶かし、鉄鋼を生産する。エネルギー消費量、CO2排出量とも大幅に削減できることが特長だ。建物の構造材などに使用するH形鋼の生産では、東京製鐵は大手高炉メーカーを凌ぎトップシェアを誇る。
岡山工場の主力製品はそのH形鋼に代表される形鋼で、他にRC構造の建築物などに使用する棒鋼などを生産する。プロジェクトでは稼働中の交流電炉(AC炉、生産能力年間85万トン)を停止し、休止中の高効率の直流電炉(DC炉、同180万トン)に粗鋼生産を集約することで、大幅なコスト削減を目指す。
計画の肝となるのがDC炉で溶解した溶鋼を受けて、中形(形鋼)工場と棒鋼工場へ鋼片を供給する連続鋳造設備の導入だ。連続鋳造設備にはDC炉の高い生産能力を受けとめるだけの世界最速級のスピードとクオリティが要求される。200トン/hを5本のストランドで鋳込むことができる世界最大級の冷却能力を有する海外製の連続鋳造機に白羽の矢がたった。
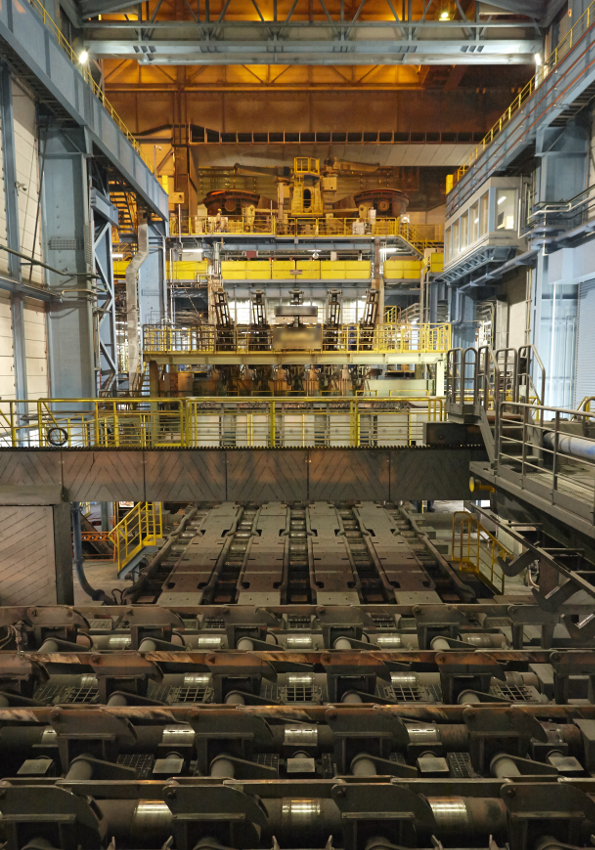
エネマネ事業者選定の決め手は大規模工場での採用実績が抜群に高いこと
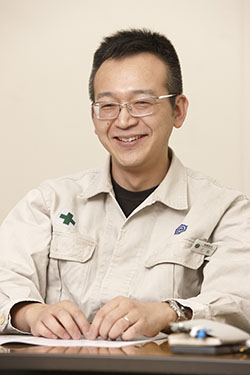
課題は、本社の決裁を得るためにも、投資回収期間を少しでも短縮することだった。プロジェクトを牽引した岡山工場生産部、製鋼課長の仁科宏隆氏は当初から以前活用したことのある「エネルギー使用合理化等事業者補助金」の補助支援を念頭に置いて、計画を進めていた。
しかし、リサーチを重ねるうちに省エネ設備+エネマネ事業者を活用した運用改善による省エネを組み合わせると、補助率を上げられることが分かった。仁科氏は早速登録されているエネマネ事業者に次々と連絡を取った。エネマネ事業者3社から提案が上がってきたが、最終的に選んだのはアズビルだった。仁科氏は「決め手となったのは、アズビルには大規模工場での採用実績があり、時間がない中、EMS(エネルギー・マネジメント・システム)による削減提案を粘り強くまとめあげたことに尽きます」と振り返る。
というのも、その時点で申請書提出期限の7月15日まで、わずか2か月しかない。しかも、EMSの公募要件となる原油換算500kl/年削減は容易に達成できる数値ではなかった。アズビルの担当者は現場に足を運び、岡山工場スタッフとともにさらなる省エネのポテンシャルを探り、削減量を見積もった。その結果、上がってきたのは電気系のインバータ制御による3案件と、今回のエネマネ事業の目玉となるLNGを燃料とする中形工場加熱炉の温度最適化制御と中形ロール組換え時の温度最適化制御。5つの省エネ案件で年間削減量553klの見積もりが立てられた。
40種類に及ぶ鋼材の品種ごとに炉内の温度を最適化制御し、ガス量を削減
加熱炉は連続鋳造機から鋼材を受け取り1,200℃に加熱し、加熱された鋼材は圧延機で加工され製品化される。温度や品種ごとに鋼材の温度を最適化制御すれば、ガス量を削減できる。しかし、加熱炉に送り込まれる鋼材は形や大きさなど品種も40種類に及び、その温度は数100℃の単位で大きく異なる。しかも、加熱された鋼材の温度を直接測定することは不可能だ。
そこで、加熱炉の入口で鋼材の温度を測定するとともに、加熱炉で加えた熱量を基に加熱炉内での鋼材(100本)一本一本の温度を見える化し、必要以上に鋼材温度が上がらないよう最適温度制御を実現することとした。
さらに圧延機では品種ごとに圧延ロールが異なるため、平均1日1~2回、1回に付き約45分かけてロールを組み替える必要がある。その待機中、加熱炉の温度を下げることができれば、大幅な省エネにつながるはずだ。そこで圧延機の再稼働時に照準を合わせ、鋼材の品種ごとにどの程度下げることができるかをシミュレーションし、設定温度を制御した。
※『エネ合補助金の変更ポイント』資料を環境ビジネス限定で無料ダウンロードできます。
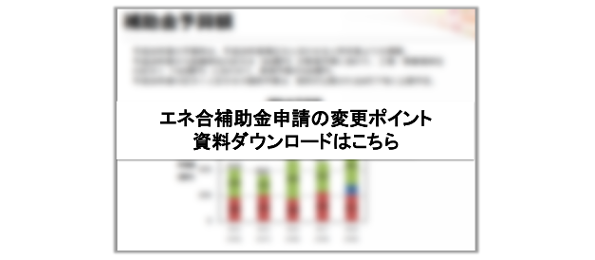

- 1
- 2